Since its foundation in 1914, Ford has driven innovation in automotive manufacturing. From inventing the moving assembly line 115 years ago – also known as Fordism – to today’s use of additive manufacturing, Ford is constantly thinking ahead to accelerate vehicle manufacture through increased productivity, ergonomics, and quality control.
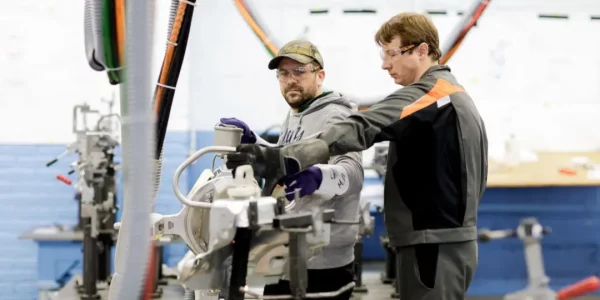
Adoption of 3D printing
Ford’s employees use many custom tools during their vehicles’ production. These are often designed for one specific task and model. Creating these tools externally takes a lot of time and is very expensive. To get tools faster, the team at Ford decided to pilot 3D printing as a possible solution.
A dedicated additive manufacturing team was founded, and they began a successful project using SLS technology. They had good results, but the prints needed some specific post-processing. That’s why Ford started using FFF technology from Ultimaker. It provided an even faster, more affordable solution with less hassle. This way, not only engineers but also local workforces are able to use a 3D printer to create the tools that they need.
Ford picked Ultimaker because the quality compared to the cost is very good and we like their reliability.
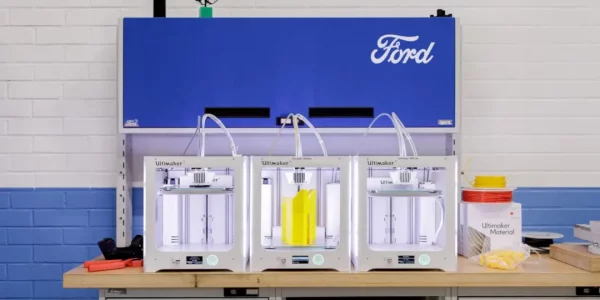
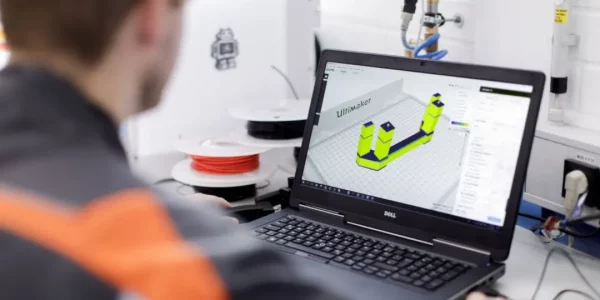
Creating tools, jigs, and fixtures before production
Many manufacturing plants implement 3D printing to optimize their current manufacturing process. However, by having a dedicated 3D workshop in the pilot plant, Ford is able to produce all the right designs before a new car goes into mass production. This gives the engineers at Ford more time to iterate the designs of all the custom tools. Ford wants to create tools which not only speed up the manufacturing time of the vehicles but also often have ergonomic benefits for the workforce. That’s why it’s important to Ford to be able to create the right design for the application.
The open filament system lets us use industrial materials which helps us to make even more durable tools and fixtures for our high volume production
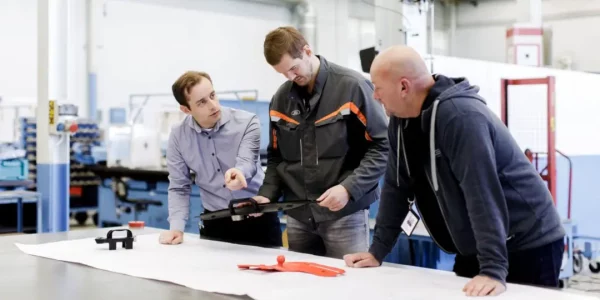
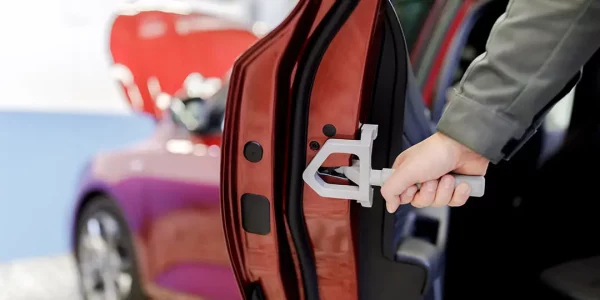
Local manufacturing
By using Ultimaker 3D printers, local workforces can also 3D print the tools they need. Ford is placing Ultimaker 3D printers in factories all over Europe, such as in Spain, Italy, and Romania. The design team in Germany will supply the designs electronically, and the tools can be used the next day thanks to 3D printing.
But Ford is also going a step further. Using Trinckle’s generative software solution Paramate, workers in these plants can generate jigs without any other experience in 3D design. The team in Cologne will create components they can use for the tools such as handles and magnet holders. The engineer will load the design of the car, add handles, an open space where they need to add a part to the car, and the software will generate the jig. This design can be sent directly to Ultimaker Cura and printed locally with their onsite Ultimaker S5 machines.
Today, only the skilled process engineers are able to design complex fixtures. In the future, even the untrained worker can use this software to create his own tools.
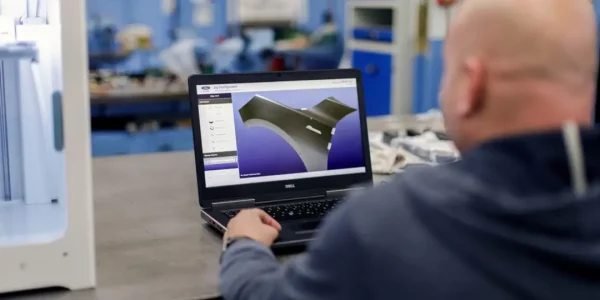
Benefits of 3D printing
So far, the pilot has already been very beneficial to Ford. Per custom tool, they save a considerable amount of money compared to traditional manufacturing or outsourcing. The Ford Focus alone is manufactured using over 50 custom designed tools, jigs, and fixtures. Ford is also looking at spare parts for production machines from the manufacturing line. By printing these parts, they drastically increase the uptime of the machines and the manufacturing line doesn’t need to be paused for lengthy periods of time.
But 3D printing isn’t just financially beneficial. Many of these tools have great ergonomic benefits for Ford’s workforce. After prolonged use, traditional metal tools can start to feel extremely heavy, and can impact workers’ health over time. Ultimaker’s range of materials are often strong enough to replace metal tools, which makes life a lot easier for assembly personnel.
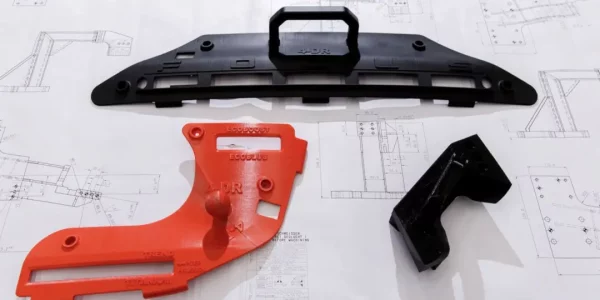
Future plans
Ford is expanding their 3D printing capabilities rapidly. While optimizing the workflow to create tools, jigs, and fixtures, they’re learning more about the possibilities of 3D printing. Lars is not only looking to create tools and fixtures, but also exploring possibilities to create spare parts and final parts using 3D printing. “We want to make the next step, we also want to 3D print spare parts. We want to design for additive manufacturing and be able to print production parts for production vehicles”.
Thinking of adding a 3D printer to your tool kit? Learn more about our most powerful 3D printer, the Ultimaker S5.