With over 150 breweries around the world, Heineken is one of the largest global producers of beer. One brewery in Seville, Spain, produces famous brands such as Cruzcampo, Desperados, Heineken, and Amstel. The beer is brewed, packed, and then shipped throughout Spain and beyond. Packaging Manager, Juan Padilla González has implemented 3D printing to increase uptime and efficiency at the Seville brewery.
Optimizing the manufacturing line
The Seville plant is able to produce up to 500 million liters of beer per year. But Heineken is always looking into new ways to improve their already impressive efficiency. That’s why they started to investigate the possibilities of 3D printing.
After setting up a 3D printing lab, the team set goals to improve the manufacturing process in terms of output, uptime, and safety. Heineken started looking for various methods of optimizing the manufacturing machines. They quickly realized that 3D printing gives them the flexibility and speed they need, while still being affordable and easy to implement.
We’re still in the first stages of 3D printing but have already seen a reduction of costs in the applications that we found by 70 – 90%, and also a decrease of delivery time of 70 – 90%.
Safety first
Employee safety is the top priority within Heineken, and they first designed improved safety latches, which are used during machine maintenance. These are applied to almost all the machines in the brewery. When the machines are stopped, these latches will be locked, preventing anyone from accidentally starting a machine while someone is doing maintenance.
The latches are printed in bright red to ensure their visibility. This application was not only useful, but the extra safety feature created awareness and appreciation of 3D printing among employees.
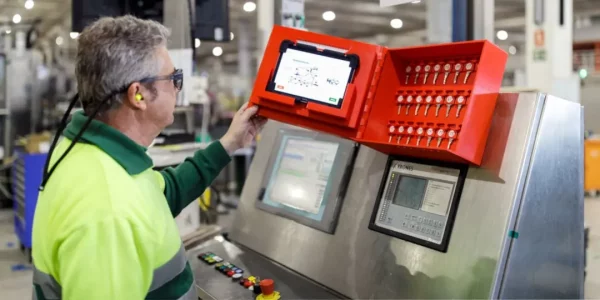
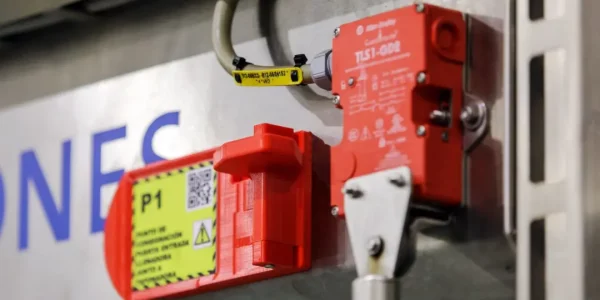
Functional parts for the manufacturing line
After the initial success of the safety latches, other 3D printed application opportunities were identified.
Ideas were investigated, and new parts designed. The first of these was to print spare parts that had proven difficult to replace. Outsourcing discontinued parts or importing them is expensive and time-consuming. The team immediately saw that 3D printing these not only saved time and money, but was also able to print plastic parts which could function as structural replacements for metal parts.
Original content by ultimaker : https://ultimaker.com/learn/heineken-ensuring-production-continuity-with-3d-printing