Two techniques have historically defined jewelry making: handcrafting and lost-wax casting. Both techniques require significant technical expertise, are highly time-intensive, and mistakes in the process can prove expensive.
But today, digital design and 3D printing are primed to disrupt these age-old practices in a major way. Supplementing traditional processes with digital techniques brings new possibilities in design and production to jewelers, as well as exciting new customization options for customers.
Digital Workflows Augment Traditional Techniques
3D printed jewelry production augments the principles of investment casting, or lost wax casting with the advantages of a digital design and manufacturing process.
With traditional lost-wax casting, jewelry designers hand-carve the original pattern in wax, place the wax pattern in a mold to be burned out, and then pour precious metals like gold or silver into the mold cavity to create the cast piece. To achieve its final appearance, designers polish and finish the cast piece to shine.
With the digital workflow, jewelers use CAD software tools to create the designs digitally and a high-resolution 3D printer to produce the 3D printed patterns that can then be cast in the mold. After burnout of the positive pattern, the process follows the same path as traditional investment casting. Thanks to the digital techniques, the need for time-intensive manual labor is reduced and the design itself is easy to preserve, modify, and recreate when needed.
How Jewelers and Customers Benefit
New Frontiers in Customized jewelry
Until now, the complexity of the design and production process made customized jewelry an expensive privilege. With digital tools, however, jewelers have already started offering personalized creations as part of their basic service or as a value add. If you go to a jeweler today and ask for an engagement ring, often you’ll have the option to customize a unique design.
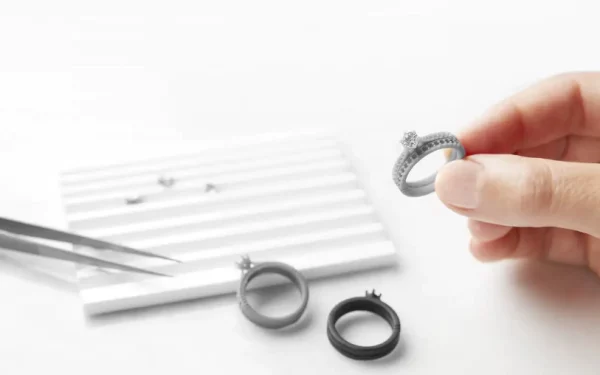
3D printed jewelry try-on pieces drastically shorten the feedback loop between designer and customer.
Jeweller and customer can discuss the design together, and an hour later, the customer can hold and try on a real, physical model of the ring. In jewelry retail, on-site digital design combined with the speed of 3D printing has drastically shortened the feedback loop between designer and customer.
Moving from design to production is easier and faster, as hand carving a precious one-off is no longer a requirement. The try-on pieces can be tailored based on the customer’s requests, 3D printed again, and then manufactured with lost-wax casting, which translates to a considerable reduction in the cost of making customized 3D printed jewelry.
Design Freedom
With 3D printing, jewelry designers are able to produce designs that would be incredibly difficult to hand carve in the traditional manner. Breakthroughs in castable resins are setting new standards for the quality available through an affordable desktop 3D printer.
3D printing jewelry patterns in Formlabs’ Castable Wax 40 Resin combines the smooth surface finish characteristic of stereolithography (SLA) 3D printing technology with precise print settings. Thanks to a precisely controlled laser, extraordinary design details—delicate filigrees, raised text, and detailed pavé stone settings—can be captured with amazing sharpness.
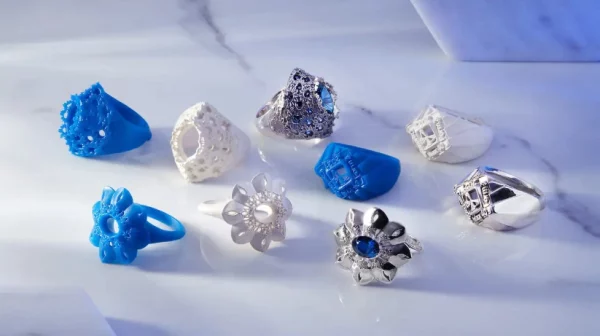
Stereolithography 3D printing can reproduce complex features that’d be difficult to hand carve.
With these long-established design restrictions now removed, we’re seeing entirely new genres of design emerging from jewelers who digital capabilities in the US as well as in South Asia and Asia Pacific, and the Middle East.
Easier Mass Production
Digital tools are not only making jewelry easier to customize, but also simpler to mass-produce designs.
Vulcanized rubber molds are used to produce wax patterns in quantity for lost-wax casting, but the “master” pattern is traditionally made from an investment cast, hand-carved wax pattern.
3D printers can produce master models that are used to form room temperature vulcanization (RTV) molds and even durable high temperature vulcanized rubber molds.
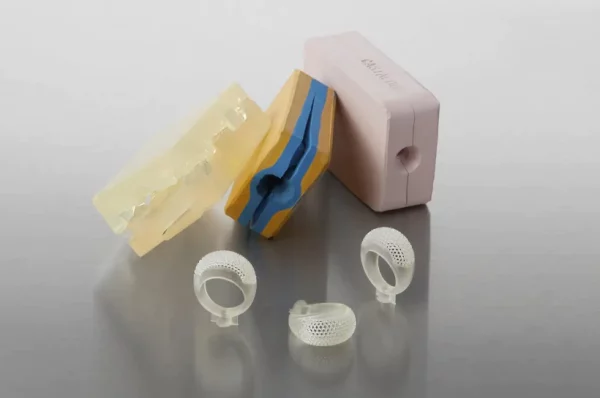
Directly 3D printed jewelry patterns can be used for room temperature vulcanization (RTV) and vulcanization of high temp natural rubber.
“With the quality that you can get with SLA 3D printing for printing these jewelry pieces, you can jump straight from the 3D printed part to a master mold,” said Formlabs’ Jewelry Vertical Product Manager Amos Dudley. “The surface finish is already so smooth that it doesn’t require very much finishing. You can use that as the rubber mold for creating the final wax parts that go into production.”
Competitive Independent Jewelers
When new technology is finally made available to the public, it usually comes with a high price tag and a complicated interface, restricting it to users with deep pockets and technical savvy. Previous generations of jewelry 3D printers required both significant maintenance and a skilled operator in addition to thousands of dollars of investment that limited them to the largest jewelry manufacturers and casting houses. Nevertheless, Dudley notes, “3D printing has become much more affordable, offering unique opportunities to independent jewelry makers.”
The lower cost and higher-quality jewelry 3D printing technology have made the digital workflow a viable method of manufacturing. “In the coming years, we’re going to see a growing trend in that segment, with smaller jewelers adopting these technologies and becoming less centralized,” Dudley said.
This shift to increasingly competitive independent jewelers will continue as the industry becomes more familiar with castable resin 3D printing. Historically jewelry 3D printing has been dominated by complex and expensive wax 3D printers. With affordable desktop jewelry 3D printers like the Form 3, the technology is becoming available to more jewelers, especially smaller independent ones.
The Future of the Jewelry Industry
Owing to the formerly high cost of large-scale 3D printing and the perceived barrier-to-entry of digital jewelry design, 3D printed jewelry, despite its potential, currently represents a relatively small fraction of the market.
Nevertheless, with increasingly easy to use and accessible 3D printing technologies, the 3D printed jewelry market is poised for growth.
New, easy-to-use materials like Castable Wax 40 Resin are easing the learning curve, leading to greater adoption of the workflow and the subsequent expansion of the market.
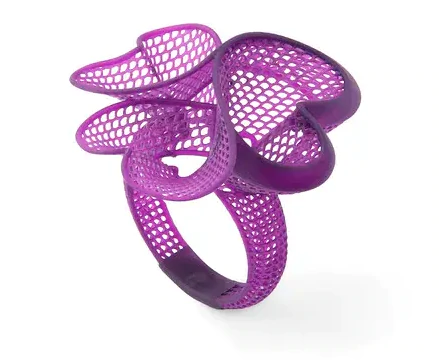
Formlabs Castable Wax Resin is filled with 20% wax to make it more reliable in investment casting.
Desktop stereolithography 3D printers are an important component in this expansion.
“SLA resins have a reputation for being cheaper, but also less functional than wax. At Formlabs, we’re looking to break that impression with products that are more foolproof and eliminate some of the extra work that’s still present in the jeweler’s workflow,” Dudley said.
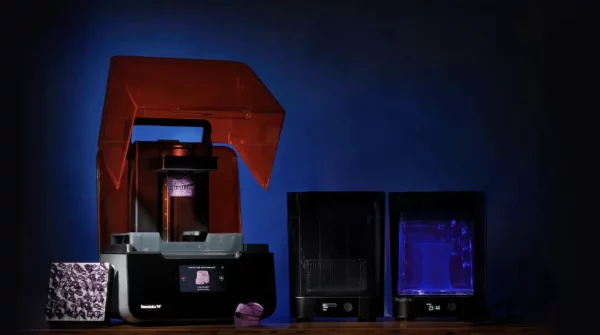
High-resolution desktop 3D printers, like the Formlabs Form 3, have made jewelry 3D printing accessible for independent designers as well as large casting houses.
3D printed jewelry is not just a matter of technology. The newer cohorts of jewelry designers entering the industry have started education with digital methods, including training on 3D printers, as opposed to the traditional ones.
“They’re going to be looking for the printer that really meets their needs,” Dudley said. “I think then we’ll start to see more adoption as they take over from the currently embedded user base.”
3D printing in jewelry has a bright horizon. With the wider industry adoption of workflow techniques, the arrival of new generations of designers skilled in them, and the creation of new, more foolproof materials and hardware, we’re seeing the stage set for a major positive disruption.
This guest post was originally published on Formlabs blog site. The content in this guest blog is for informational and educational purposes only and may contain copyrighted material from Formlabs.
Source: Formlabs