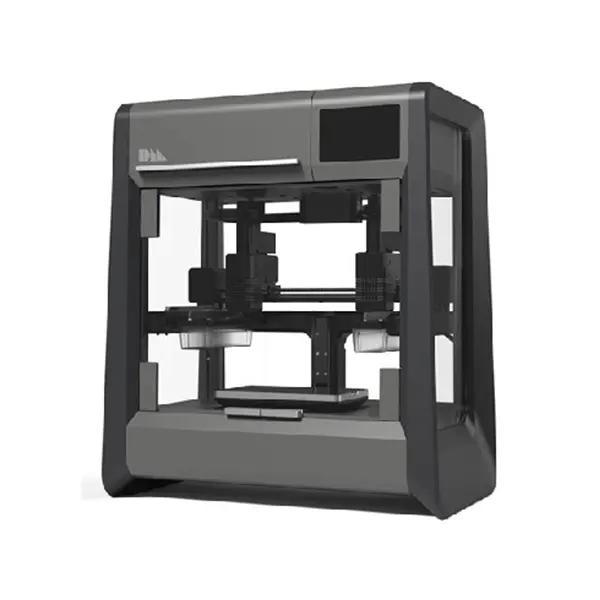
Desktop Metal Studio System 2

Office-friendly Metal 3D Printer designed for ease of use. Studio System 2 allows you to spend less time managing equipment and more time designing and fabricating parts
Unlike comparable metal 3D printing systems, Studio System™ 2 eliminates loose metal powders and features a two-step process (no solvent debind required) and features Separable Supports technology with strategic splits for hand-removable supports, hot swappable cartridges and removable printheads to make material changes easy, and a fully software-controlled workflow.
Desktop Metal Studio System 2

Office-friendly Metal 3D Printer designed for ease of use. Studio System 2 allows you to spend less time managing equipment and more time designing and fabricating parts
Unlike comparable metal 3D printing systems, Studio System™ 2 eliminates loose metal powders and features a two-step process (no solvent debind required) and features Separable Supports technology with strategic splits for hand-removable supports, hot swappable cartridges and removable printheads to make material changes easy, and a fully software-controlled workflow.
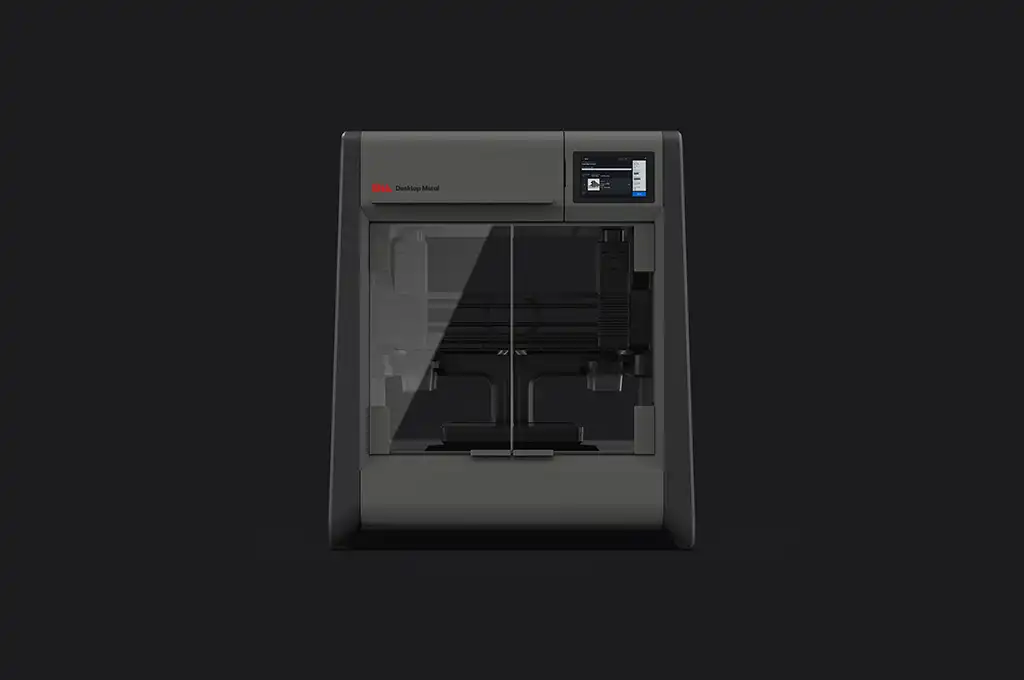
The Studio System™ 2 is the easiest way to print high-quality metal parts in your office. Leveraging an all-new material system, the Studio System™ 2 eliminates the Debinder (and solvent debind step), unlocking a drastically simpler and more hands-off workflow. Parts no longer need to be batched before debinding, and then batched again before sintering. Now, making metal parts is a simple two-step process that offers improved first-time part success and outstanding surface finish on side walls and support-facing surfaces across a wider range of complex geometries.
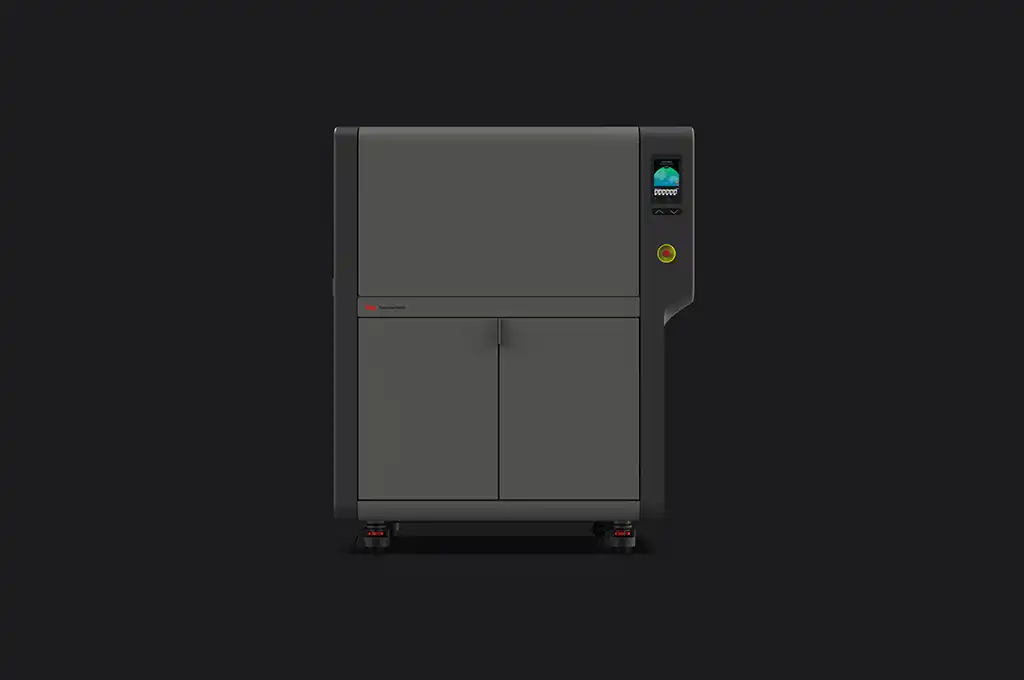
We are excited to bring the Studio System™ 2 capabilities and workflow to your existing Studio System or Studio System+ through the simple upgrade process detailed below.
Unlike comparable metal 3D printing systems, Studio System™ 2 eliminates loose metal powders and features a two-step process (no solvent debind required) and features Separable Supports technology with strategic splits for hand-removable supports, hot swappable cartridges and removable printheads to make material changes easy, and a fully software-controlled workflow.
Studio System™ 2 upgrade
Any existing Studio System™ or Studio System™+ can be upgraded to Studio System™ 2. In order to support the new material system and move parts through the simplified two-step process, minor hardware upgrades are required for the Printer and Furnace. These upgrades must be performed by a certified Desktop Metal service technician (through your local reseller) and include the components below.
Hardware upgrade
Studio System™ or Studio System™+ Printer and Furnace hardware will receive an upgrade to bring them to the Studio System™ 2 functionality. Notably, additional heaters are added to the internal plumbing of the Furnace to enable processing the new material systems. The upgrade contains the following items:
- Printer and Furnace hardware upgrade
- Printheads (standard resolution and interface)
- Media and interface cartridges + refills (316L v.2 and interface v.2)
DM Care
In order to upgrade to Studio System™ 2, your existing Studio System™ or Studio System™+ must be covered by a DM Care contract for at least 6 months past the date of purchase of the upgrade. For example, if you have 3 months remaining on your DM Care contract, you must purchase at least an additional 3 months of DM Care along with the upgrade. If your existing Studio System™ or Studio System™+ has at least 6 months of DM Care remaining on the contract, no additional purchase of DM care is necessary. If you have no DM Care coverage for your existing system, you must purchase at least 6 months of DM Care coverage.
Service visit
The upgrades must be performed by a certified Desktop Metal support technician, which may incur a charge to cover the service visit.
Timing
Upgrades are available for purchase starting February 12, 2021.
Studio System™ 2 launch material - 316L stainless steel v.2
316L stainless steel is the first material to be released for Studio System™ 2. This highly alloyed stainless steel has material properties surpassing MPIF-35 minimum specifications and is a great choice for general functional prototyping and the creation of jigs and fixtures. We’ve found some key applications in the creation of fluid manifolds, food and chemical processing, and manufacturing aids. The “v.2” materials are a new class of materials that go directly from the printer to the furnace. The v.2 materials use a new polymer binder system that is only removed with heat in the furnace.
Along with 316L v.2, we are also releasing a new Interface v.2 with Studio System™ 2. This interface contains a “v.2” binder system, making it compatible to print alongside other v.2 materials. Furthermore, the new Interface v.2 incorporates the latest in Separable Supports technology and is designed to more closely match the shrinkage of the printed metal part in the furnace, enabling first-time part success on geometries that were previously not possible.
As an added benefit, 316L v.2 and Interface v.2 rods can be purchased and shipped separately from the cartridges themselves. Rods are shipped in a media refill pack via parcel directly to your doorstep (as opposed to freight shipment). Once you receive the rods, you can simply load them by hand into the media cartridge. That media cartridge can be used over and over, eliminating the waste of empty media cartridges.
The following media refill packs and cartridges are now available. Note, that these are included in the Studio System 2 upgrade, and extra quantities can be purchased separately.
- Metal v.2 media cartridge (BMD-MP2101): single, empty and refillable cartridge used for metal material
- Interface v.2 media cartridge (BMD-MP2100): single, empty and refillable cartridge used for interface material
- 316L v.2 media fill (BMD-MP2002): package of vacuum sealed 316L v.2 rods used to refill the metal cartridge. Qty: 192 rods / 810cc of material (for reference, the current cartridges contain 200 rods / 840cc).
- Interface v.2 media fill (x4) (BMD-MP2000): package of vacuum sealed rods used to refill the interface cartridge. Contains enough rods to refill the interface cartridge 4 times. Qty: 64 rods / 270 cc of material (for reference, the current cartridges contain 18 rods).
Questions and answers
Other 3D Printers by Desktop Metal
Filaments