restor3d is on a mission to empower healthcare providers who repair and reconstruct the human body. It has pursued an approach driven by additive manufacturing due to the design freedom and affordability of 3D printing, which offers a path to disrupt traditional medical markets. The restor3d team drives innovation in precision surgery by changing the way both implants and surgical instruments are developed and delivered.The company was co-founded in 2017 by distinguished entrepreneur, orthopedic surgery professor, and highly-cited materials scientist and engineer Ken Gall.
restor3d leverages 3D printing capabilities to drastically improve surgical care delivery by printing procedure-specific polymer instrumentation that is tailored to cervical spine implants. With over 132,000 anterior cervical discectomy and fusion (ACDF) procedures performed per year in the United States1, this massive market traditionally uses stainless steel instruments. These traditional instrumentation systems are slow to evolve, have significant upfront costs, and often present complications in the surgical workflow.
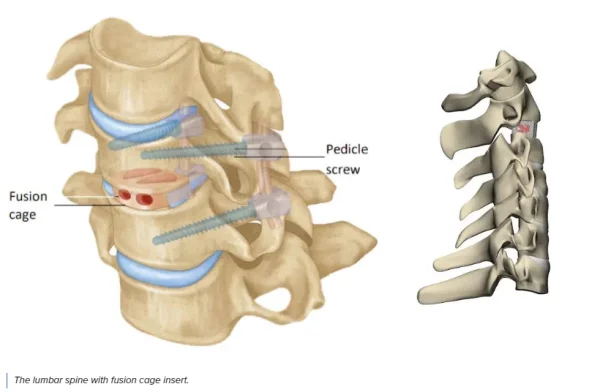
With a fleet of over 25 Formlabs 3D printers in its production line, restor3D is already printing the next generation of surgical tools. This procedure-specific, single packed sterile instrumentation system result in:
- Replacement of large, expensive surgical trays.
- Ability to iterate designs and quickly introduce new tools or features based on surgeon preferences.
- Dramatic reduction of supply chain and sterilization costs for hospitals.
We spoke with Cambre Kelly, VP of Research and Technology at restor3d, to understand how the team tackled this ambitious endeavor, why they invested in Formlabs 3D printers, and understand what is next for restor3d.
A New Frontier of Surgical Instrumentation
restor3d is comprised of a team of highly skilled biomedical engineers and material scientists who initially focused on 3D printed implants for cervical spine surgeries. But in developing these new implants, the team kept running up against a recurring issue: traditionally manufactured stainless steel instrument systems.
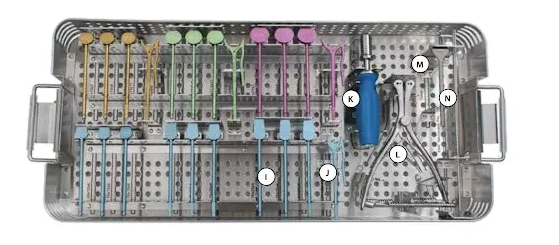
A traditional surgical tray. Source and © : Zimmer Biomet
Kelly explained the situation, saying, “we were developing an innovative implant that has features that are only achievable with 3D printing, but expecting surgeons to use a very traditional instrument system to deliver the implant. So we realized pretty quickly that evolving the instrument offering alongside the implant innovation was going to be an important differentiator for us.”
Kelly continued, “we are uniquely capable of delivering true just-in-time products because of our in-house manufacturing and the ability to quickly tune design and geometry based on feedback from the field. Traditional instrument trays are typically machined from stainless steel, and cost upwards of $50,000 per tray. As a medical device manufacturer, if you’re going to make the investment into buying 10 instrument trays at $50,000 each, you’re going to be locked into using those for a really long time. You’re really not going to be willing to iterate the design, throw away a tray, and start from scratch or change some seemingly small features. On the other hand, because of what we’re doing with directly printing single-use instruments, we’re able to iterate and revise our designs pretty nimbly.”
Creating single-use, procedure-specific, surgeon-matched tools required a truly agile development process, closing the gap between surgeon feedback and product development to an extent not previously attempted. restor3D knew surgeons might be hesitant to change their tools; not every surgeon was trained the same way, changing habits is hard, and experienced surgeons may have their own techniques honed over decades of work.
Because of these concerns, restor3D works closely with orthopedic spine surgeons to quickly turn around new tools based on their feedback. By deploying a truly agile and integrated development process, powered by the same in-house 3D printing technology for R&D and manufacturing, the team is able to deliver nimble and precise instrumentation, freeing surgeons from traditional trays that are typically updated every few years at best.
To get a clinical perspective, Formlabs spoke with Dr. Erik Westerlund, a fellowship-trained orthopedic surgeon who specializes in spine. Dr. Westerlund has been highly impressed with the first generation ACDF system created by the restor3d team, saying “the current development process has been the same for the last 20 years. A company has a new implant and/or instrument system. The company shows up, does some prototyping, and a few days or weeks later there is something to look at. Several weeks later a beta instrument shows up. But now, restor3D isn’t turning out a prototype in a few weeks, they’re turning out the real instrument in a few days. To me, that completely changes what is possible.”
He continued, “it’s not just the implants that are important, but the implants and the implant technique. That’s what makes a successful procedure. This new approach by restor3D is a systems approach. Using additive manufacturing, there is integrated parity between the implant and the instrument – the ability to change both to create the best outcome for the patient.”
Dr. Westerlund sees an opportunity to not only replace old instrument systems, but also to create new ones that exceed what was possible before. Working with the restor3D team, his input has been critical in designing and developing the new instruments. What’s exciting for him is not just the use of 3D printing in manufacturing, but the capable team restor3D has assembled around the technology, saying, “I feel like someone just took the handcuffs off of us. Most companies are still approaching this as rapid prototyping, not rapid instrument manufacturing – that mindset is completely disruptive, and you need an engineering team built around it to make it happen. This is very disruptive, from an instrument standpoint, because you can start thinking how this completely changes traditional approaches to implant and instrument systems.”