With features such as multiple lenses, image stabilization, and advanced software, modern smartphones can produce images that rival the quality of professional cameras.
The mission’s result? The Quad Lock Vibration Dampener, a mount for motorcycles that both stabilizes and protects smartphones. It features a dual-chassis suspension system with precision-engineered silicon grommets that absorb vibrations, reducing more than 90% of the high-frequency vibrations produced by motorcycles.
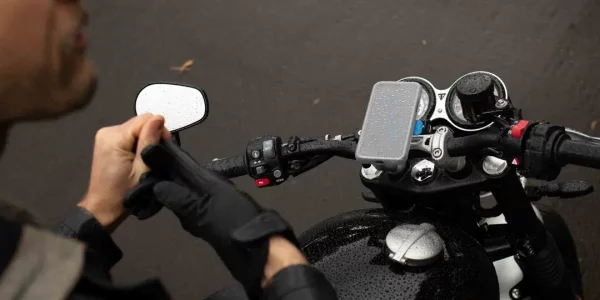
The Quad Lock Vibration Dampener features a dual-chassis suspension system
Designing the Quad Lock Vibration Dampener
For the Quad Lock team, the first step in designing the Quad Lock Vibration Dampener was to create a method that could repeatedly reproduce the real-world vibrations of a motorcycle. To do so, the team analyzed users’ riding behaviors and patterns, and worked with leading vibration experts to develop a testing method.
This method became a tool that enabled the Quad Lock team to create designs targeting specific frequencies. What eventually became the Quad Lock Vibration Dampener was successfully put through rigorous performance testing, with the final design being extensively tested by the device’s end users.
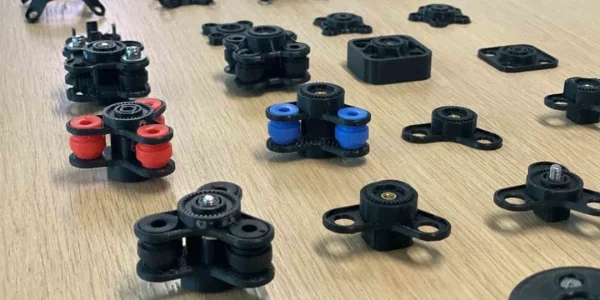
Design iterations for Quad Lock’s smartphone mount
Overcoming validation challenges
To gather feedback and quickly implement it into design iterations, the Quad Lock team needed to create physical components that were strong enough to be used on test rigs and real-world applications, opening the door for 3D printing technology – specifically the Ultimaker S3, Ultimaker 3, and Ultimaker 2+.
The Quad Lock Vibration Dampener’s product development process consisted of two main phases: rapid concept iteration and real-world testing. More than 100 iterations of the design were produced, each testing factors such as the impact of dimensional changes, clearances, and material durometers.
This high turnover rate allowed the team to gather feedback, implement it, and produce the next iteration as cheaply and quickly as possible – with multiple iterations sometimes being produced in the span of a single day.
These designs were strong enough to withstand hours of testing on a vibration test rig, from which the team gathered valuable feedback and data. This kept the team’s morale and motivation high, and helped them streamline their production workflow, saving time and money.

The Quad Lock Vibration Dampener reduces more than 90% of the high-frequency vibrations produced by motorcycles
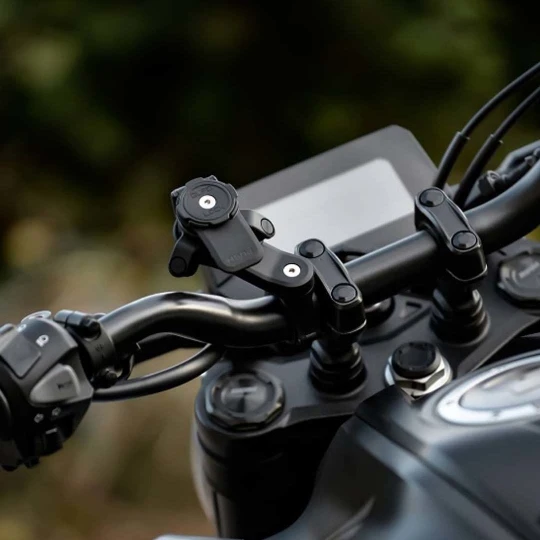
Precision-engineered silicon grommets absorb vibrations and protect smartphones
A ‘fully embedded’ design process
Today, Quad Lock’s production facility is responsible for products distributed to millions of international customers. Additive manufacturing technology is now fully embedded in Quad Lock’s design, prototyping and production processes. This greatly benefits the company as it expands its product range, with mounting solutions for cars, runners – even interior walls of houses or office buildings.
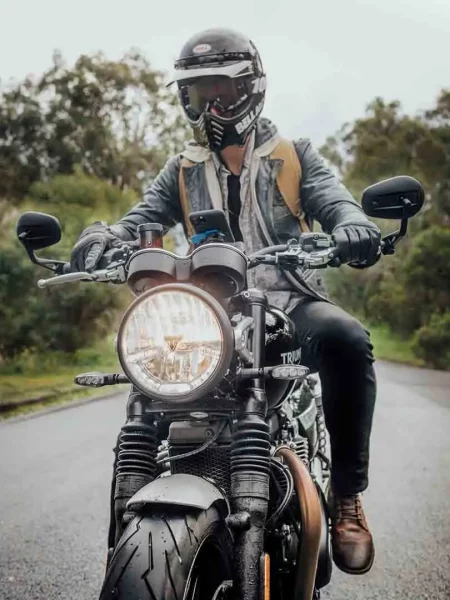
On the road with the finished product